Neodymium Permanent Magnets for New Energy Automobile 20170824
With simple structure, high power density and light weight, high performance neodymium permanent magnet synchronous motors become main choice of new energy automobile motors. Comparing with other types of motors, with same weight and volume, PM synchronous motors can provide the biggest power output and accelerated speed. Meanwhile, due to strict requirements of space and weight, mostly new energy automobile manufacturers use permanent magnets in synchronous motor. Despite magnetism recession under high temperature, shaking and overflow, 90% of new energy automobiles in the world employ permanent magnet synchronous motors, except Model X and Models. Model 3, put into mass production by Tesla in July, also uses rare earth neodymium permanent synchronous motor, which indicates these motors fully occupied new energy automobile market.
A fully electric vehicle consumes 5-10kgs of high performance neodymium magnets, a plug-in hybrid electric one 2-3kgs and hybrid power one 1-2kg. Globally, NdFeB magnets for new energy vehicles will estimated reach 9206 tons and 11876 tons in 2017 and 2018, with 25% and 29% year-on-year growth, according to two hypothesizes that output of PHEV and EV will increase by 35% and 40% and PHEB products increase by 15% and EV, PHEV and EV will relatively consume 7.5kgs, 2.5kgs and 1.5kgs of neodymium rare earth magnets.
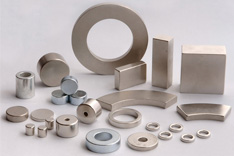
A fully electric vehicle consumes 5-10kgs of high performance neodymium magnets, a plug-in hybrid electric one 2-3kgs and hybrid power one 1-2kg. Globally, NdFeB magnets for new energy vehicles will estimated reach 9206 tons and 11876 tons in 2017 and 2018, with 25% and 29% year-on-year growth, according to two hypothesizes that output of PHEV and EV will increase by 35% and 40% and PHEB products increase by 15% and EV, PHEV and EV will relatively consume 7.5kgs, 2.5kgs and 1.5kgs of neodymium rare earth magnets.